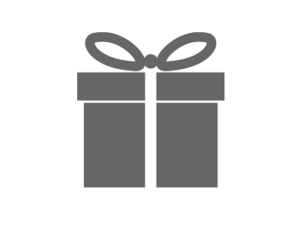
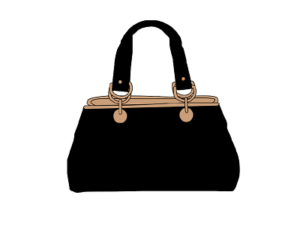
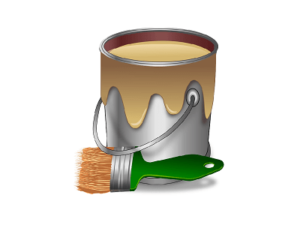
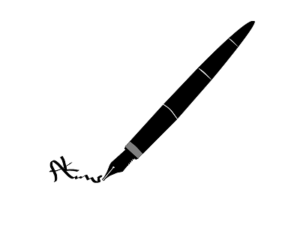
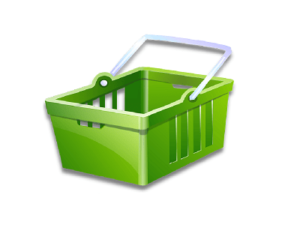
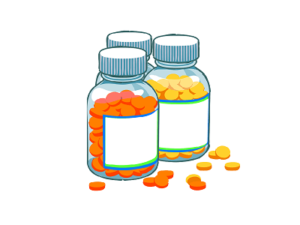

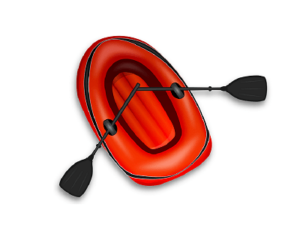


“Shutdowns are a concern for companies like Huntsman and also for retailers,” Schlaefke says. “You can imagine retailers have contracted with a fabric-producing mill—they negotiated six months ago and agreed on a price—but suddenly that price is not certain anymore. It’s not a crisis, but it makes business a little more complicated for everyone.”
The largest impact of the factory shutdowns has been in the supply and price of so-called disperse dyes, which are used to color synthetic fibers like polyester, a specialty of Chinese producers, Schlaefke says. Availability of reactive dyes, which are used on cotton, was also reduced, though manufacturers in cotton-rich India are likely to take up the slack.
In India as well, the government is taking steps to reel in the textile industry to save precious water resources. “In India, a trend is huge investment in wastewater treatment for liquid discharge,” Schlaefke says. It’s now common for factories to reuse 90% of their water. While both cotton and polyester are normally colored with synthetic dyes, dyeing cotton is a more water- and heat-intensive process. The surface of cotton fibers is negatively charged and doesn’t readily react with negatively charged dye compounds.
Even with an assist from salts and alkali added to the dye solution, cotton takes up only about 75% of the dye. To ensure colorfastness, dyed fabric or yarn is washed over and over again in hot water, creating large amounts of wastewater.
All told, about 200 L of water is used to produce 1 kg of fabric. A review of wastewater treatment steps found that textile effluent contains high concentrations of dyes and chemicals, including chromium, arsenic, copper, and zinc. Dyes and chemicals released into waterways also block sunlight and increase biological oxygen demand. Bleeding and crocking: Two components of colorfastness. Bleeding happens when dye comes off a fabric in contact with liquid. Crocking occurs when a dye on a dry fabric rubs off on another dry fabric.
Colorfastness: The ability of a dye to preserve the original color during industrial processing and subsequent customer use. The American Association of Textile Chemists & Colorists provides several dozen test methods to ensure colorfastness of dye products.
Digital textile printing: Directly printing colors and patterns onto fabric using design software, large-format printers, and specialty inks made with pigments or dyes. Digital printing is an alternative to standard screen printing, which uses a constrained color palette and requires separate stencils and production steps for each color.
Dye: Soluble chemicals that contain chromophores, or color-containing compounds. Dyes are mixed with other additives in a color solution. They can be derived from natural sources, such as plants, but are more commonly human made. Different classes of dyes are used for different fibers and stages of the textile production process.
Direct dye: A class of dye that can be applied directly to cotton or other cellulosic fabrics such as rayon, silk, and wool. Direct dyes are applied in a neutral or alkaline bath of hot water. They do not require mordant or fixatives for fastness; instead, they attach with hydrogen bonds and van der Waals forces. Direct dyes are soluble salts of complex sulfonic acids, including diazo or polyazo chemicals. Disperse dye: A category of nonionic dyes used to color synthetic yarns and fabrics such as polyester. These organic chemicals, mostly monoazo dyes, are nonsoluble and rely on dispersing agents to spread the color molecules in water.
Reactive dye: A class of colored synthetic organic chemicals that attach to textile fibers via a chemical reaction that forms a covalent bond. Reactive dyes are the most permanent of all dye types and are the most common type of dye used on cotton and other cellulose fibers. They are categorized by their functional group, such as dichlorotriazine or vinyl sulfone.
Dye exhaustion or dye fixation: The mass of dye taken up by the yarn or fabric divided by the total initial mass of dye in the water bath. Once the dyeing process reaches equilibrium, a portion of the dye remains in the dye bath and becomes part of the dye process wastewater. The exhaustion ratio depends on the quality of the dye and the characteristics of the fiber.
Leveling agent: Used in disperse dyeing to regulate or slow the uptake of dye onto synthetic fibers to ensure that the color level is uniform. Leveling agents are often nonionic surfactants that increase the solubility of the dye and slow adsorption.Mordant: Also called a dye fixative, a substance used to chemically bond a dye to natural fibers to ensure fastness. Mordant chemicals include alum, caustic soda, and metal salts. The mordant forms a coordination complex with the dye, increasing its molecular weight and making it insoluble.
Pigment: Insoluble materials, usually in powder form, that add color to inks, paints, plastics, cosmetics, and foods. When used on textiles, they require binders or other additives to attach to the fibers. Pigments can be derived from minerals but can also be made synthetically. Because they are not soluble in water, they can last longer than dyes.